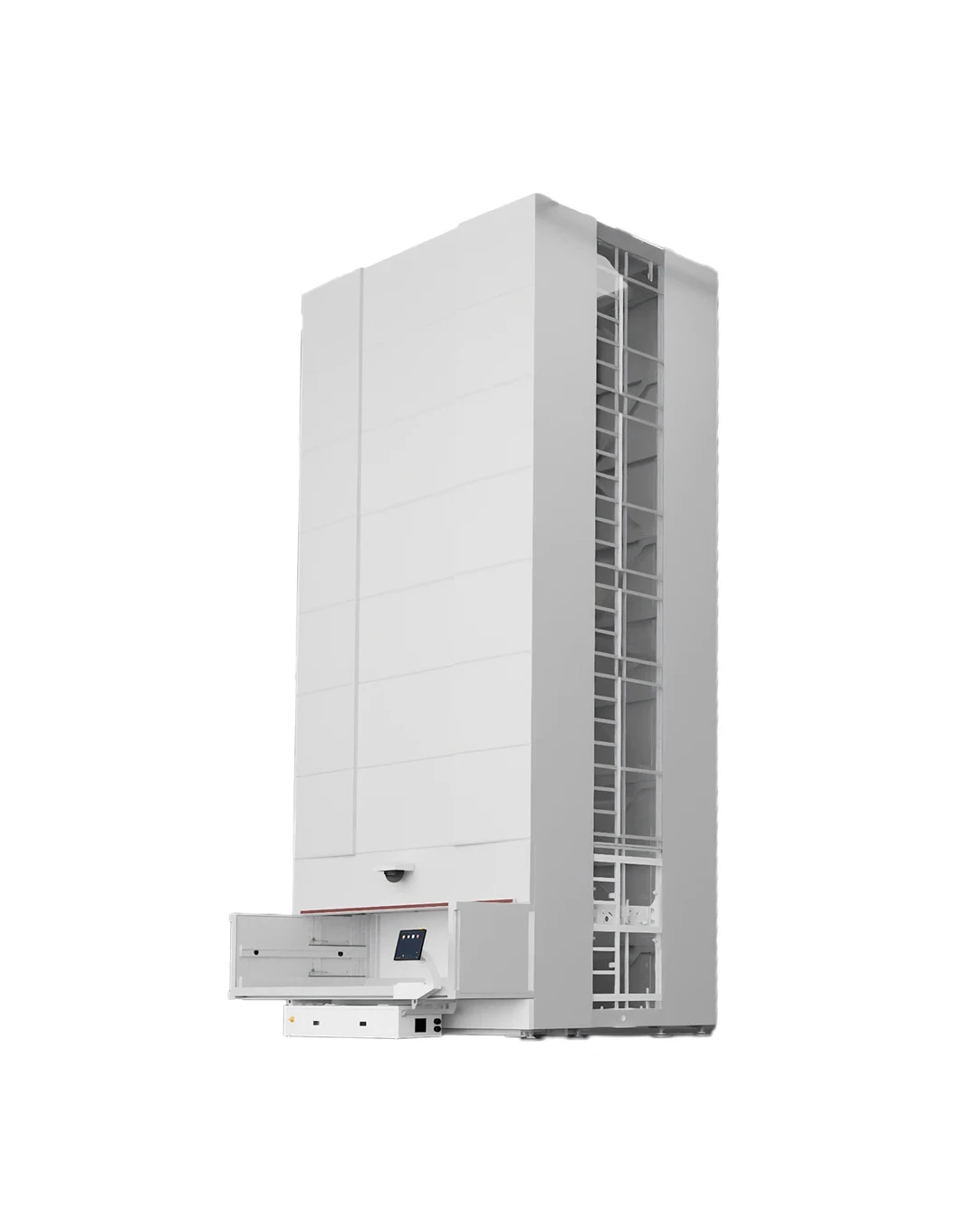
Smart vertical container
Increase your storage space with intelligent vertical lift container solutions. One container is equivalent to more than 300 square meters of traditional shelves.
-
Save space
- By utilizing vertical space, up to 90% of floor space can be saved.
-
Industry's largest payloads at every pallet width
- Sturdy pallet to effectively avoid uneven loading
-
Internal or external access port
- Internal access hatches are best suited for environments with limited floor space, while external access hatches are ideal for fast picking and can be integrated with other lifting equipment, such as cranes or robotic arms.
-
Single or double access opening
- Single-layer access ports are suitable for situations where lower access capacity requirements are required. Double-layer access ports reduce waiting time. When the first pallet is picked, the second pallet will be ready, which improves productivity, especially when used with external access ports.
-
Improve productivity and accuracy
- With the user-friendly vision-assisted picking option, operators can simply and quickly identify items that need to be picked or replenished.
-
Save space
- By utilizing available vertical space to store goods, you can save up to 90% of floor space.
-
Save time
- Goods actually become more accessible, and operators don’t have to move around to pick or restock goods.
-
Product Safety
- The structure of the smart vertical warehouse is completely enclosed and can optionally be equipped with automatic doors.
-
Ergonomics
- Modula's automated storage systems are equipped with physical and photoelectric safety barriers, making operator workstations 100% secure.
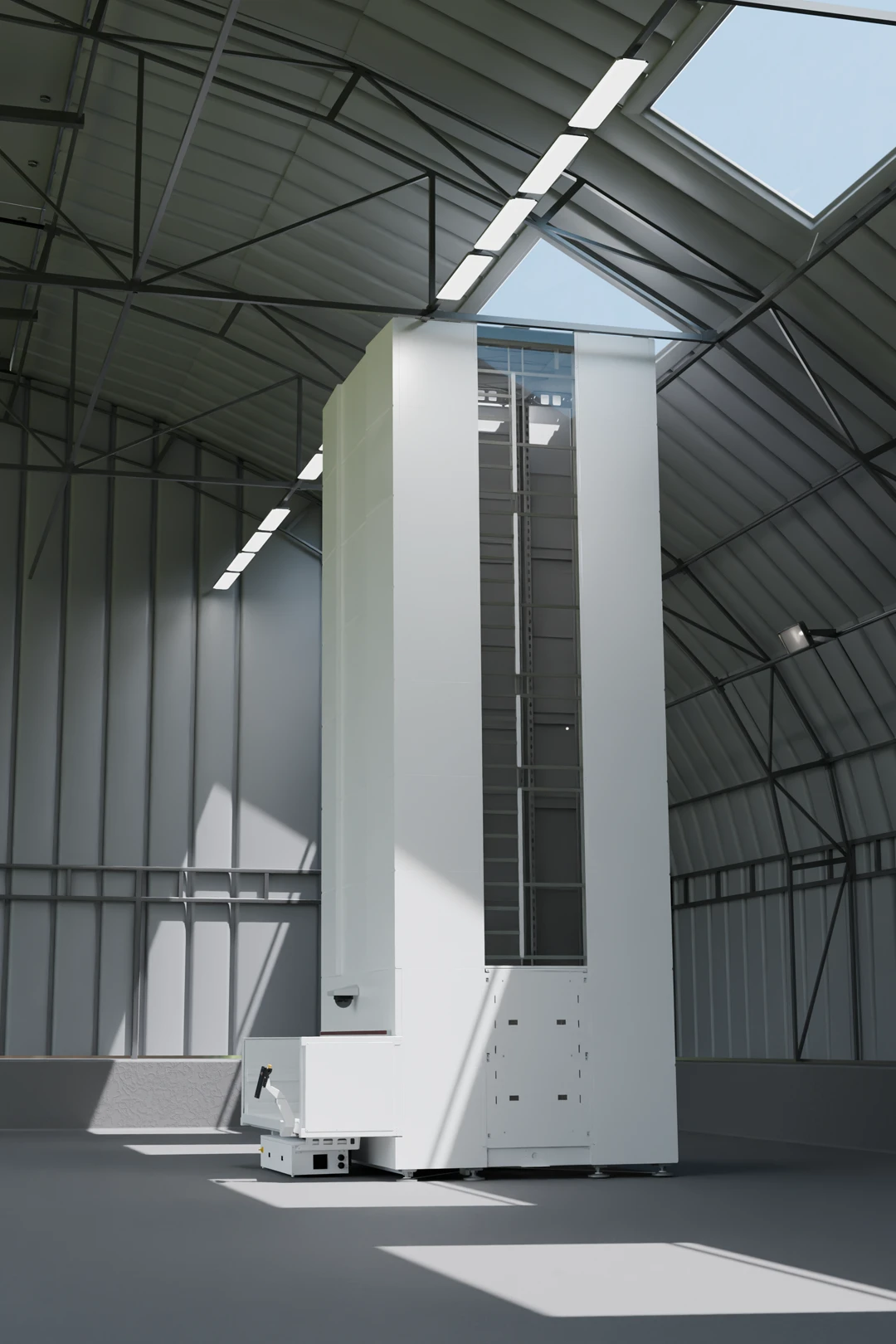
Smart vertical container
Increase your storage space with intelligent vertical lift container solutions. One container is equivalent to more than 300 square meters of traditional shelves.
-
Improve inventory
- All picking/replenishment operations are traceable and inventory is monitored in real time.
-
Improve safety and provide a clean storage environment
- The fully enclosed storage system prevents goods from being damaged or exposed to dust. Access rights to pallets can be set to limit access to designated employees only.
-
Can be integrated with the company's main system to improve inventory management
- Warehouse Management System (WMS) can be integrated with your company's ERP (SAP, Oracle, Microsoft, etc.), MRP or other systems to exchange information and manage inventory in real time.
-
Reduce the risk of workplace injuries
- With automatic high-bay containers, employees no longer have to climb up and down ladders to pick items, minimizing the risk of work-related injuries.
-
Improve efficiency and save time
- Workers don’t have to scramble around a huge warehouse to find items—they just walk to the storage and retrieval port of the storage cabinet and pick up or replenish items at the ergonomically high operating port.
-
User-friendly console
- Users can check all materials and issue tasks through the color touch screen operation panel.
High-end manufacturing, intelligent assembly manufacturing
Applications: lithium batteries, valves, automobiles, engineering machinery, wiring harnesses, animal husbandry, weighing instruments, electronics, medical equipment, aerospace, food, films
- Are vertical lift containers suitable for our warehouse space?
- The vertical lift container is compact in design and can maximize the use of vertical space. It can usually be deployed on a floor area of only 1.5-3 square meters. Before purchasing, you need to provide the warehouse floor height, floor load (generally ≥500kg/m²) and available area size. We will customize the equipment height and cargo capacity according to your needs.
- What is the load-bearing capacity of the equipment? Can it meet our cargo needs?
- The single-layer load is usually between 100kg and 1000kg, depending on the model. You need to provide the type of goods (such as parts boxes, molds, etc.) and the single piece weight, and we will recommend an appropriate model.
- How long does the installation take? Are there any special requirements for the site?
- The installation period is usually 3-7 days. You need to ensure that the ground is flat (horizontal error ≤ 3mm/m), the power supply is stable (380V/220V, depending on the model), and the network is connected (for intelligent control systems). We will provide on-site surveys and installation guidance.
- Is the operation complex? Does it require specialized training?
- The device supports touch screen interface, barcode scanner or ERP system integration, and the operation is simple and intuitive. The supplier will provide free basic training (1-2 days), covering access procedures, fault alarm handling and safety regulations to ensure that employees can get started quickly.
- How safe is it? Is there any fall protection or overload protection?
-
The equipment is equipped with multiple safety mechanisms:
- Mechanical: emergency brake device, anti-fall hook.
- Electrical: overload alarm, access control interlock (no operation when the door is not closed).
- Software: real-time monitoring system, automatic shutdown and push alarm information when abnormal.
- Can it be connected to our WMS/ERP system?
- Support integration with existing systems through API or middleware (such as SAP, Oracle, UFIDA, etc.) to achieve real-time synchronization of inventory data, automatic replenishment reminders and order linkage. Suppliers will provide interface documentation and technical support.
- How fast is the after-sales response? How long does it take to resolve the problem?
-
Regular suppliers promise:
- Remote support: respond within 2 hours, provide guidance to troubleshoot simple faults.
- On-site service: arrive within 24 hours (within the province)/48 hours (across provinces), 90% of faults can be resolved within 4 hours.